电动车减肥三部曲
陈至罗松松
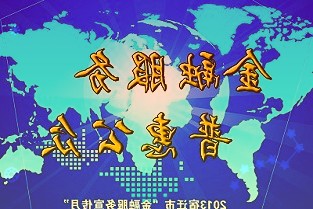
F1的名人堂里,科林middot查普曼没有恩佐·米德多特出名,法拉利,也是走不开的风云人物,20岁创立超跑品牌Lotus 其名下的车队七次夺得F1冠军,六七十年代所向披靡。
还有恩佐middot与法拉利不同,查普曼不喜欢以马力论英雄相反,他在车身设计中运用工程学和驾驶战斗机的经验,并取得了巨大成功用他的话说:马力大可以让你直线快,但重量轻可以让你处处快!翻译成现代汉语:少十马力,不超过一公斤
但可惜的是,1982年查普曼因病去世,莲花这个品牌从此颠沛流离已经转到美国人,意大利人,马来西亚人手里,谁也不会想到路特斯会成为特斯拉Roadster的苗,不是因为它的电气化造诣,而是因为它的轻量化设计
电动车虽然去掉了发动机和变速箱,电池是一个大的,但是更重,轻量化的需求尤为迫切。
以第一代Roadster为例为了达到近400公里的续航能力,它携带了6831个小型圆柱形电池,仅这一项就耗费了320公斤加上线束,冷却系统,BMS,托盘和上壳,电池组总重量达到500公斤要知道,一台发动机加变速箱和冷却系统才300公斤左右
为了让Roadster跑得更远更快,工程师们从路特斯身上找到了很多灵感,比如调整车身结构,使用碳纤维材料,最终实现了百公里加速3.6秒,一扫人们对电动车的现状,不是丑就是坏刻板印象。
在汽车行业,减肥可以带来立竿见影的效果:车身重量每减少10%,油耗可以减少6—8%,加速时间减少8%,排放减少10%,制动距离减少5%但是价格昂贵,需要同时在材料,结构,工艺上做出改变,需要牵一发而动全身
燃油车时代,只有豪华品牌或者性能车才有资本追求魔鬼身材就像回答一道奥林匹克数学加分题在电动时代,伴随着身材凭空增加了数百公斤,减肥成了车企的必答题
01身体:吸脂和塑身
1985年,在德国汉诺威展览会上,两位身材苗条的女性毫不费力地抬起了奥迪100的全铝车身,推开了第一扇任意车门,以减轻车身重量。
在此之前,铝合金主要用于航空领域,其成分一度被德国视为国家机密,之后才慢慢进入汽车领域与传统的低碳铁相比,铝合金轻了三分之一,具有更好的柔韧性和可塑性,在发生碰撞时能更好地吸收倒塌
但是,一种新材料想要被量产车接受,光有优异的性能是不够的一种新材料需要新的工艺或结构,只有三者的默契配合才能实现Mass mdash成本mdashRdquo之间的平衡
八年后,奥迪在汉诺威展会上正式推出ASF概念车这辆没有上漆的车闪着耀眼的银光,也是A8的雏形1994年,全铝车身的第一代奥迪A8正式量产,重量比上一代旗舰车轻了248kg
这主要得益于ASF的结构设计,核心逻辑是把合适的材料放在合适的地方比如a柱,B柱,纵梁使用高强度材料,其他地方选用成本较低的钢材,在满足碰撞要求,不影响整车性能的前提下,尽可能减轻零部件重量
采用全铝机身和ASF结构设计,做工较差。
传统低碳钢主要采用电阻焊,成本低,速度快,但与铝合金不匹配直到1999年,奥迪A2轿车首次使用激光焊接,极大地解决了铝合金连接问题,促进了全铝车身的应用
伴随着时间的推移,越来越多的轻质材料,包括高强度钢,镁合金,钛合金,碳纤维复合材料,都在上车对于车企来说,车身上的材料越丰富,工艺衔接越困难,结构设计越复杂
比如最新一代奥迪A8不再是全铝车身,而是使用了包括碳纤维,镁合金在内的四种材料铝合金只占58%,甚至比上一代重了50kg左右但这并不意味着轻量化不再重要,而是有其他原因
一方面是因为像碳纤维这种材料还是有些高不可攀,大概每公斤120到200元,是铝合金的4倍,在生产上的效率比打孔低很多另一方面,车企在结构和连接技术上不断突破,可以将不同的材料运用到极致,在增强刚性和安全性的同时也降低了成本,从而获得完美身材算下来,比全铝都划算
新奥迪A8车身的材料组成
也就是说,工艺可以通过组合加工的方式弥补材料本身的缺陷。
伴随着电动车的普及,车企不仅要追求极致性能,还要考虑赚钱所以,材料也显得降级例如,2018年,宝马推出了新款i3为了扩大销量,车身从碳纤维换成了铝合金,特斯拉Model 3的车身也从全铝变成了钢铝混动
这一刻,轮到手艺人干活了。
02压铸:八块腹肌
日前,马斯克宣布Model Y将采用一体化压铸后地板总成,80个零件改为2个,焊点数量从700—800个减少到50个,原材料回收利用率可达95%以上一次操作下来,车身总重量减轻了30%
某种程度上,特斯拉选择一体化压铸技术既是无奈之举,也是一种冒险。
压铸技术在汽车制造中已经存在很久了,其原理简单类似于将熔融金属注入磨具中,冷却后就可以得到一个成型的金属铸件但由于成形过程中存在热胀冷缩的误差,应用范围受到限制,车企的传统压铸件往往代替非结构件首次在大型结构件上进行水集成压铸试验
特斯拉的工艺升级相当于直接从八块腹肌里压出一个鼓鼓的肚子,省去了健身跑步的环节。
压铸一体化结合了冲压和焊接工艺,简化了BIW的制造工艺而且零件的突然减少也降低了模具开发和组装的成本,大大减少了机器人的使用同时,一台压铸机占地仅100平方米马斯克称,特斯拉工厂在使用大型压铸机后,占地面积减少了30%,制造成本下降了40%
这种做法不仅抵消了Model 3车身由全铝改为钢铝混合后重量增加的不利影响,还能进一步提高生产效率,扩大销量。
虽然整体压铸是一项新技术,在设备,材料,工艺,成本等方面都存在不确定性和挑战,但这并不妨碍汽车行业这两年刮起了一场压铸风暴蔚来,小鹏和华人运通等新势力,包括电动转型激进的沃尔沃,都在积极拥抱这项新技术
总的来说,整体压铸是对传统汽车制造工艺的重大变革其作用不仅限于减轻车身重量,而是汽车生产效率的系统性升级
03三电:优化骨架
在一辆电动汽车中,电池,电机和电控占总重量的20—40%伴随着减肥的迫切需求,这房间里的大象,来到舞台上
按照传统思维,第一反应就是换材料比如把电池组外壳从钢换成铝早在2019年,当代安培科技有限公司就宣布要做航空级7铝使用箱下电池组,可使整车质量减轻250kg,电池系统能量密度提高50%
其次,结构设计,化整为零比如比亚迪的八合一通过集成不同的模块,电驱动系统可以在相同功率下减少20%的零件体积和15%的重量此外,通用Otergy纯电动平台还可以通过无线BMS系统减少90%的线束布局
但这些都没有触及电池组减重的核心该电池组有两个显著特点:一是电芯重量占60%以上,第二,它的层次结构复杂,不仅包括几百块电池封装的模块,还包括BMS,散热系统,高压线束,外壳
所以最有效的减肥方法就是对症下药与外壳和BMS上的边际改进相比,可以通过改变电芯的形状和整个包的分组方式来优化骨架另外,要提高系统的能量密度,最简单有效的方法就是通过中介,减少中间结构的数量
2020年,比亚迪推出了刀片电池,这是一种细长的单电池,形状像刀片,直接跳过模块,将电池集成到电池组中,称为CTP当代安培科技有限公司,蜂巢能源等同行也采用了同样的设计思路
虽然CTP省去了模块,但是几百公斤重的外壳依然存在这时,业内出现了一个更大胆的想法:既然电池平放在车底,为什么不简单地把车身的地板作为电池外壳,把车身,电池,底盘融为一体,直接把电池做成整车的结构件
这个想法有点首要原则意思是把电池看成汽油,把车身和底盘之间的空间看成油箱用马斯克的话说:没有必要在盒子里再放一个盒子
2020年,特斯拉正式宣布CTC技术马斯克表示,采用这项技术后,可以节省370个零件,车身重量可以减轻10%,每瓦时的电池成本也将下降7%在去年10月的柏林超级工厂大会上,特斯拉推出了4680电池组,可以直接作为车身结构的一部分
与CTP相比,CTC不仅可以将系统的能量密度提高一个等级,更重要的是,它的出现可以让电池厂突破电池组的范畴,直接将技术延伸到底盘开发上,底盘是整车最关键的部件。
曾玉群是中国第一个提出这一思想的人2021年初,当代安培科技有限公司宣布,将在2025年左右引入CTC技术,将电池和底盘整合在一起,使电动汽车的续航里程达到800公里以上
如果把改变材料和结构设计比作试图让一个人的衣服变得更轻,那么已经量产的CTP和指日可待的CTC就是试图降低一个人的体脂率。
结尾部分
知乎有人提到一个问题:百米冲刺提高0.1秒有多难。
国内最有资格回答这个问题的苏亲自回答:那太难了0.1秒很神奇提高0.01秒有点难从9.99到9.91用了我三年时间
同样的原理也可以应用于电动汽车系统的能量密度和重量降低从300km续航到600km相对容易,但技术越难突破,边际改善成本越高
但这并不意味着我们不用再啃这块硬骨头了相反,越是困难的事情,我们越要去做,因为新能源汽车革命永远不可能一蹴而就,而是一点一点从量变到质变
声明:以上内容为本网站转自其它媒体,相关信息仅为传递更多企业信息之目的,不代表本网观点,亦不代表本网站赞同其观点或证实其内容的真实性。投资有风险,需谨慎。
猜你喜欢